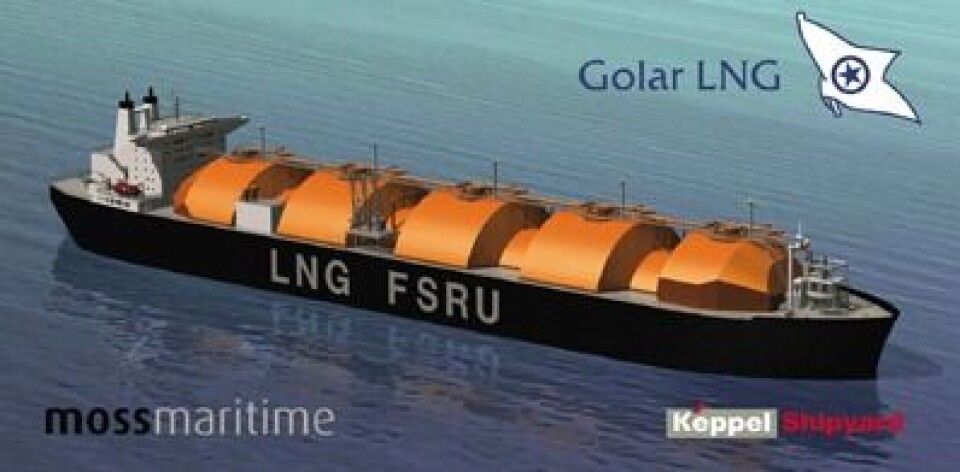
The world's first LNG Floating Storage and Regasification conversion
Golar LNG Limited and Keppel Shipyard Limited of Singapore have signed a contract for the first ever conversion of an existing LNG carrier into a LNG Floating Storage and Regasification Unit (FSRU). The total contract value is approximately US$90 million.
Denne artikkelen er tre år eller eldre.
Keppel Shipyard Limited is the leading ship repair yard for Liquefied Natural Gas (LNG) and Liquefied Petroleum Gas (LPG) carriers outside Japan. Moss Maritime of Norway (a Saipem company) has prepared the conceptual specification for the FSRU and will carry out the design and engineering.
When the conversion is completed in the second quarter of 2007, it will be the first of its type in the world. The conversion will be made based on relevant DNV class rules and international standards.
Golar LNG will work in partnership with Keppel Shipyard in the engineering, procurement and construction for the project. The scope of work includes installation of new forward turret, side-by-side mooring system, LNG loading arms, aft thruster with compartment, a regasification plant and replacement of cargo pumps. There is also upgrading of the existing steam power electrical and marine systems. The full concept is based on well proven and working technology.
Mr Graeme McDonald, Group Technical Director of Golar LNG said – Golar LNG has been developing this "Floating Energy Solution" as part of our strategy to diversify into other parts of the LNG value chain. It is our belief that no other system can compete with this concept in terms of timing or pricing when satisfying early or extra demand for gas.
– Our market survey has discovered several specific opportunities for the FSRU, however no fixed employment contract has been signed. The relative pricing differential between LNG and oil and the increased overall energy demand in developing nations gives us some very interesting opportunities.
– Calculations completed for potential clients show that the Golar terminal can be available approximately three years ahead of a conventional land based terminal and that the annual savings in overall energy production cost can be more than USD 50 million. Furthermore this commitment by Golar LNG has the dual advantages of locking in a start up date for a project and thus allowing potential end users to make firm preparations and commitments. In the past the lack of such firm commitment has delayed progress in a number of projects."
– We have selected Keppel Shipyard as our partner due mainly to the company's impressive track record and proven experiences with Moss Rosenberg type LNG vessels.
Mr Nelson Yeo, Executive Director of Keppel Shipyard, said – Being entrusted to undertake the world's first FSRU conversion certainly strengthens our market leadership in offshore and marine conversions, especially in the areas of LNG vessels. We are committed to deliver the facility on time, on budget.
Keppel Shipyard
has a strong track record of repairing 71 vessels of Moss Rosenberg type LNG vessel. The largest LNG repair yard outside Japan, Keppel has also completed 54 FPSO/FSO conversion projects to date.
The proposed LNG terminal is a steel mono hull with Moss LNG tanks arranged in the middle, with the re-gasification plant in the forward section and crew facilities with control room and utility machinery in the aft section.
The LNG offloading tankers will be moored in a side-by-side configuration with the FSRU for efficient replenishment of the terminal.
The FSRU will be stationed offshore and, through a subsea pipeline, will be capable of a throughput of 2.75 BSCM per annum at variable gas send out pressures up to 85 bar.
Golar LNG/Keppel O&M
Golar LNG is the largest independent LNG ship owner and currently owns a fleet of 11 vessels with two more on order. Golar operates vessels worldwide in well-established relationships with British Gas, Pertamina, Chinese Petroleum Corporation, Petronas, Sonatrach, and Shell.
A member of Keppel Corporation Limited, Keppel O&M is a global leader in offshore rigs and ship conversion and repair as well as a specialised shipbuilder. Combining the expertise and experience of its subsidiaries, Keppel FELS, Keppel Shipyard and Keppel Singmarine, the group's near market, near customer strategy is bolstered by a global network of 17 yards in the Asia Pacific, Gulf of Mexico, Brazil, the Caspian Sea, Middle East and the North Sea regions.
Integrating the experience and expertise of its yards worldwide, Keppel O&M aims to be a provider of choice and a partner in solutions for the offshore and marine industry.
Data
The LNG storage capacity will be 129,000 m3 with a design life of 20 years based permanently moored. The unit can operate on water depth between 50 and 150 metres.
The vessel was built in 1981 with a length over all of 289 metres and a breadth moulded of 44.60 metres. The terminal shall allow safe berthing of standard LNG carriers. Assuming the terminal is being served by ship size of 125,000/137,000 m3 the arrival schedule will be about every nine days.
The terminal will be fitted with an azimuth thruster for control during LNG carrier berthing and unberthing. During berthing the cargo tanker will need the assistance from two tugs with minimum 50 tons bollard pull.
The FSRU will be provided with standard loading arms to allow side-by-side transfer of LNG and vapor return. Operation with two LNG arms will ensure a loading time of 16 hours. Berthing, loading and unberthing will take approximately 24 hours.
LNG is sent from the tanks to the regasification skid situated forward. The regasification skid essentially comprises booster pumps and steam heated vaporizers. The booster pumps will increase the pressure to about 90 bar before the high pressure LNG is vaporised, after which the gas passes through a fiscal metering unit and is sent to the sub sea pipeline via the gas swivel and flexible risers.
Maximum gas send-out pressure is 85 bar and maximum gas send-out flow is 240 t/h.
The existing equipment shall be used for onboard power generation. There are two steam driven turbo generators onboard, and in addition one larger steam driven turbo generator of about 6MW will be installed. Further, there is a diesel driven generator as well as a diesel driven emergency generator.
The boilers will run on natural gas only, supplied by suction of BOG from the vapor header and partly by addi
tional fuel supplied by the LNG vaporizers.
Another jackup rig order
Keppel FELS Limited (Keppel FELS) has received notice from Sinvest ASA’s wholly-owned subsidiary exercising its option signed in February 2005 for another KFELS Super B class jackup rig. To be completed in first quarter 2009, the rig is contracted at around US$140 million.
This KFELS Super B Class jackup is Sinvest’s fifth rig with Keppel FELS and can drill high pressure, high temperature wells up to 35,000 ft at 350 ft water depths.
Sinvest’s first rig with Keppel FELS is expected to be delivered in April this year, while the next three rigs will be progressively delivered between end 2006 and third quarter 2008.
Involved primarily in investments relating to the offshore industry, Sinvest ASA is a public company quoted on the Oslo stock exchange.