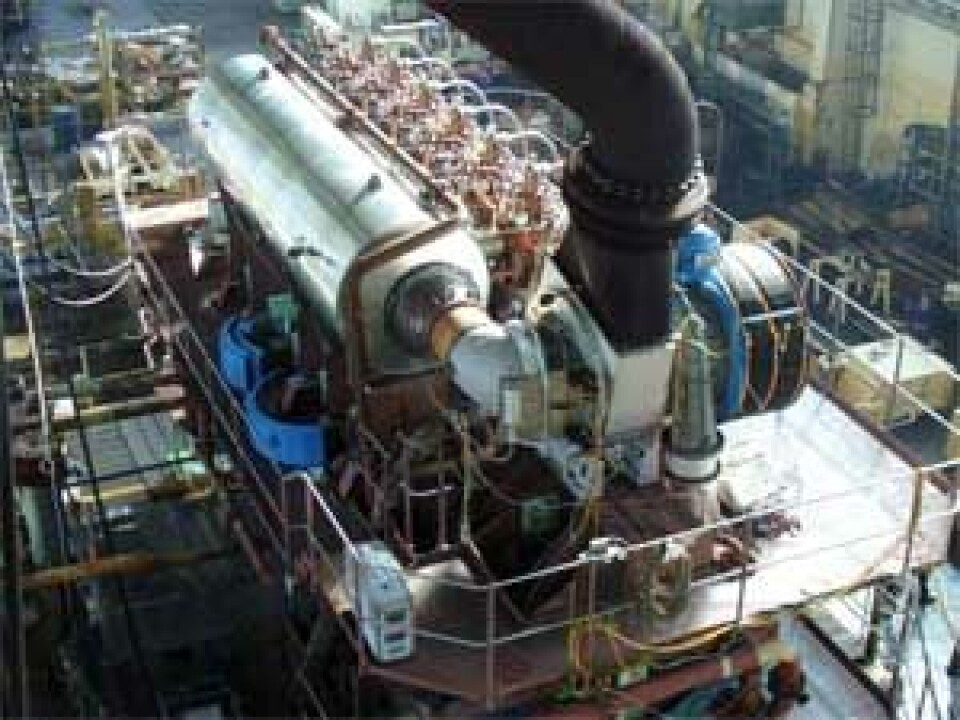
Advanced turbocharger technology central to future development of large diesel and gas engines
The next phase of diesel engine development is set to be dominated by advanced digital electronics as the enabling technology of the highly flexible setting of engine operating parameters. On the fuel management (injection) side, the advent of microprocessor-controlled common rail fuel injection technology has given the designer the scope to optimise injection pressure and timing at any point on the operating profile of a large diesel engine. Paralleling this development, the Business Unit Turbocharger at MAN Diesel in Augsburg, Germany, is pursuing projects aimed at achieving a similar level of parameter control on the air management side.
Denne artikkelen er tre år eller eldre.
At the “Turbocharger Technical Update” event held in Augsburg in mid December 2007, the Business Unit Turbocharger gave an exposé of its current development activities in the area of advanced turbocharging for large two- and four-stroke diesel engines. A traditional turbocharging pioneer, MAN Diesel has never relinquished technological leadership since it began turbocharger manufacturing in 1934. For example, only a few years later, in 1940, MAN Diesel devised the basic rotating group concept that would come to predominate in all sizes of turbocharger – i.e. a core group consisting of the turbine and compressor mounted either end of a shaft supported in a central “inboard” plain bearing, lubricated from the engine lubricating system. This concept was - sooner or later – adopted by all major manufacturers.
Emissions and fuel consumption
At the centre of present development activity is planned legislation to further limit emissions of oxides of nitrogen (NOx) from large diesel engines, as exemplified by the second Tier of emissions regulations from the International Maritime Organisation (IMO) and similar limits for stationary engines, as well as efforts to reduce specific fuel oil consumption (SFOC), both for economic reasons and as a route to reduced emissions of the greenhouse gas carbon dioxide (CO2). Indeed, the link between fuel efficiency and emissions has gained new importance as emissions of CO2 have come to share equal focus with noxious emissions like NOx and oxides of sulphur.
While, essentially, exhaust emissions are in direct proportion to fuel consumption, a special challenge in reciprocating engines is the so-called “trade-off” between specific fuel consumption and NOx – i.e. the fact that reducing NOx formation in diesel or gas engines is normally bought at the expense of fuel efficiency.
Inclusion of VTA technology on the axial TCA55 turbocharger allows up to 0.5 bar variation in compressor output pressure at part load. Overall results show the expected improvements at part load in terms of fuel consumption, as well as considerable reductions in emissions of soot and unburnt hydrocarbons, as well as improved engine response under load changes. It was also demonstrated that VTA technology gave a useful new dimension to the mechanically controlled engine. The effects are comparable to the use of variable valve timing and
High pressure turbochargingComplete article with illustartions, see Skipsrevyen 1/08.