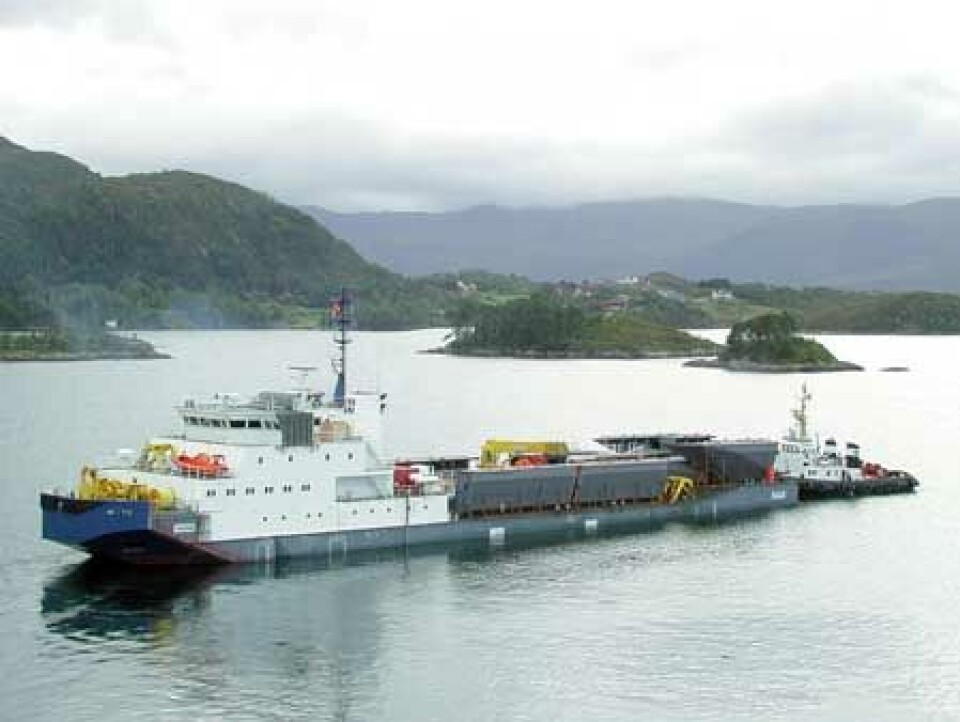
Sailing Safely through the Ice of the Caspian Sea
With enormous power, they plow an open water path through the forbidding ice: Ice breakers must therefore withstand amazing forces and be equipped with the most advanced technologies. In the Caspian Sea too, these wide-bodied ships use their massive hulls to break ice sheets apart. To make such amazing feats possible, Voith Turbo recently supplied its Type 1150 TM1-X Turbo Couplings to an offshore supply vessel powered by Schottel Rudderpropellers.
Denne artikkelen er tre år eller eldre.
Conventional ships usually try to avoid any contact with ice or pack ice. However, if they are forced to sail in ice-covered waters, they follow in the path of an ice breaker. Thanks to an ice breaker’s reinforced hull, the double-welding of its outer joints and its extra strong bulkheads, they are ideally suited for their difficult mission of opening ice-bound channels. To clear the widest possible shipping lane, ice breakers also have an unusually wide hull. Their bows too are specially designed – having a relatively flat, cambered form for crushing the thick ice rather than cutting it with a sharp edged bow.
Ice breakers therefore push their hulls up and on to an ice sheet so that the weight of the ship can be used to break through the ice. By improving the bow’s shape, today’s modern ice breakers only need engines with half as much power as older models.
The Caspian Sea however,
which borders on Turkmenistan, Iran, Azerbaijan, Kazakhstan and Russia, presents ice breakers with special challenges. Extremely shallow waterways with depths of only 3.5 meters and 75 cm thick ice sheets in the winter are two major problems. As a result, determining the correct power rating for an ice breaker’s propulsion system is extremely difficult and despite the best efforts, overloading and jamming of a ship’s propeller often occurs. These are also the challenging waters where the ice breaker M/V “TULPAR” operates with its Voith Type 1150 TM1-X Turbo Couplings, which provide the ship’s propulsion system with an extra measure of safety and reliability, as well as absorbing vibrations, reducing noise and improving its maneuverability.
The Voith Turbo Couplings, installed between the electromotor and the Schottel Rudderpropellers, allow the propulsion system to reach its full operational capability (net power 2,000 kW, net rotational speed 1,200 1/min, net torque 15,900 Nm).
During start-ups, the electromotor must exert significant force to accelerate the stationary propeller. This however is where the advantages of the Turbo Coupling come into play: it ensures that the motor is not suddenly overloaded by the full starting torque, and it allows the propeller/driveshaft to gradually reach its operating speed. As a result, frequent start-ups are no longer a problem and the motor’s operating life is significantly extended too. When maneuvering, these Turbo Couplings have a maximum transmission-slip of only 2 %.
When sailing through ice fields, the torque exerted on the propellers often increase suddenly. This is why the frequency converter is designed to permit an excess-torque of 110 %, before it reduces the system’s rotational speed. Here, the hydrodynamic Turbo Coupling transmits the required torque to the propeller and it also absorbs most torsional vibrations. In addition, the coupling reduces the impact caused by a jammed propeller during ice breaking operations: thereby protecting the propulsion system, improving its reliability and raising the ship’s overall safety level. When faced with a sudden overload, these Turbo Couplings respond with an extremely flat power curve gradient. Even during extreme variations in torque, it is the coupling’s speed that varies and not the motor’s. Thanks to the coupling’s slip ratio, sudden overloads can therefore be trapped and absorbed while the motor maintains a constant speed – which means the propeller speed can be immediately accelerated once the cause of the overload has been passed. Plus, when the Turbo Coupling is not in operation its fill-volume can be adjusted to accommodate special operating conditions – making these couplings user-friendly, easy for new crew members to operate, and increasing the overall level of safety for everyone onboard.