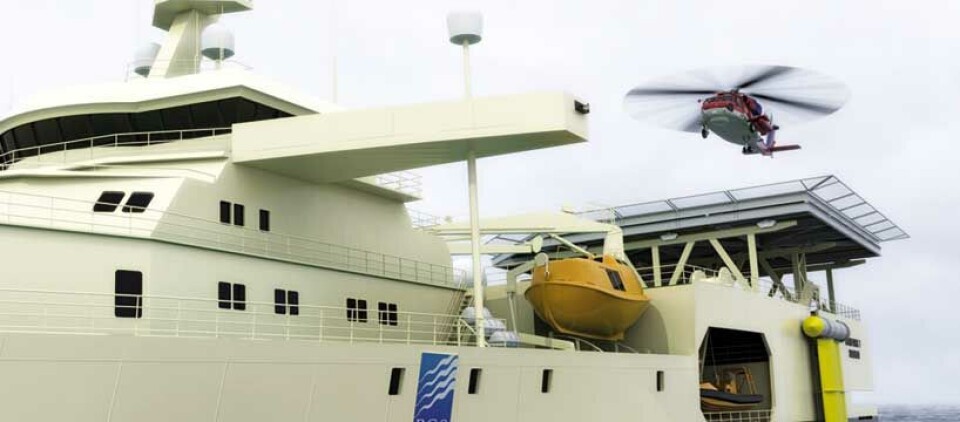
Landing Safely on a Rolling Ship
Try jumping from one boat to another on the open sea: Only experienced seamen can instinctively manage it – at least most of the time. Landing a helicopter on a ship deck, however, is incomparably more demanding – unless, that is, the ship’s helicopter deck is equipped with an active roll compensating system with hydraulic controls from Rexroth.
Denne artikkelen er tre år eller eldre.
Landing on a rolling ship is the perfect plot for a high suspense computer game, but in real life helicopters bring in crew members and valuable supplies. First the pilot has to adopt the speed of the ship. Now comes the tricky part: Due to the rolling of the ship the helicopter platform moves continuously several meters from one side to the other.
The helicopter’s center of gravity during landing is at the top directly beneath the main rotor, making it vulnerable to any side movement. When the surface of the platform is slippery due to unfavorable weather conditions, the helicopter might slide side-ways. When the platform is dry, the high friction may cause it to roll over.
Expanding the operation window
To expand the window of operation at sea, Norwegian TTS Offshore Handling Equipment AS has developed a fully automated Active Roll Compensated (ARC) landing platform. The hydraulic control solution for this system was developed by TTS OHE supported by an international Rexroth team. One major advantage:
Having already gained considerable knowhow from being involved in numerous projects for the marine market in Norway, the specialists from Rexroth understood the challenges.
TTS-OHE has already installed the first ARC platform on the “Ramform Sovereign”, the world’s largest and most advanced seismic vessel. The ship, built by Aker Yards, is 102 meters long with a gross tonnage of 15,000 tons. Directly after the ship’s launch in 2008 owner and operator, Petroleum Geo-Services, was awarded a contract by a Brazilian company to undertake the largest seismic survey ever in the off-shore oil and gas industry.
Safety first
For each ship regulations permit helicopter landings only up to a certain rolling angle of the ship. In the North Sea without the ARC platform this is limited to two degrees, but even then the platform still rolls several meters from port to starboard.
Two hydraulic cylinders with a 4.4 meter stroke placed beneath the platform move the 26 x 26 meter sized steel platform compensate the rolling of the ship at a speed of up to 1.6 m/s. The cylinders are controlled in real time by a high-end motion control MAC-8 and customized valve blocks. For calculating the compensation, two motion reference units constantly measure the ship’s angle of dip. Based on this data, the superior control system transmits in real time a position value to the MAC-8. The motion control synchronizes the two cylinders via high response proportional valves with on board electronics. The TTS-OHE specification asked originally for a maximum deviation of less than 50 millimeters between the two cylinders. The Rexroth motion control achieves a 10-fold higher accuracy, keeping the deviation at 5 millimeters.
The design gives safety in operation highest priority. TTS-OHE opted for a redundancy of all critical components with the exception of the cylinders. The superior control system developed by TTS-OHE can switch jerk free between the running motion control and the redundant electronics. The two MAC-8 motion controls are connected to the control system via CANOpen and via the specified analog voltage to the valves with on board electronics. A valve block on each cylinder with two customized high response proportional valves includes separate locking valves as an additional safety feature.
Roll angle of up to five degrees
Each MAC-8 sends all error and status information to the control system, including a "life"-bit signalizing the status of the controller. In the event of an error in the active motion control, the control system switches the access rights to the second Mac-8, simultaneously including a signal to the isolator valves regarding the change. This happens so fast that the cylinders have a minimal jerk.
For the commissioning and adjustment of the ACR system Rexroth specialists are working on board the “Ramform Sovereign” together with the team from TTS-OHE. The first goal for the project is to increase the tolerated dip angle for safe helicopter landing by 50 per cent from 2 to 3 degrees. The more ambitious goal: Compensating even 5-degree angles, so that helicopters can land safely on the rolling ship even when bad weather last for weeks.